740 EP Mortar 25 Patch Kit
740EP Mortar 25 Patch
RECOMMENDED FOR:
Recommended for cold storage areas, freezers, walkways and support bases for tanks and seamless floors.
NOT RECOMMENDED FOR:
Immersion applications for live solvents.
STANDARD COLORS:
Light gray, Red, Dark Gray, and Natural.
PRIMER:
None required.
TOPCOAT:
None required.
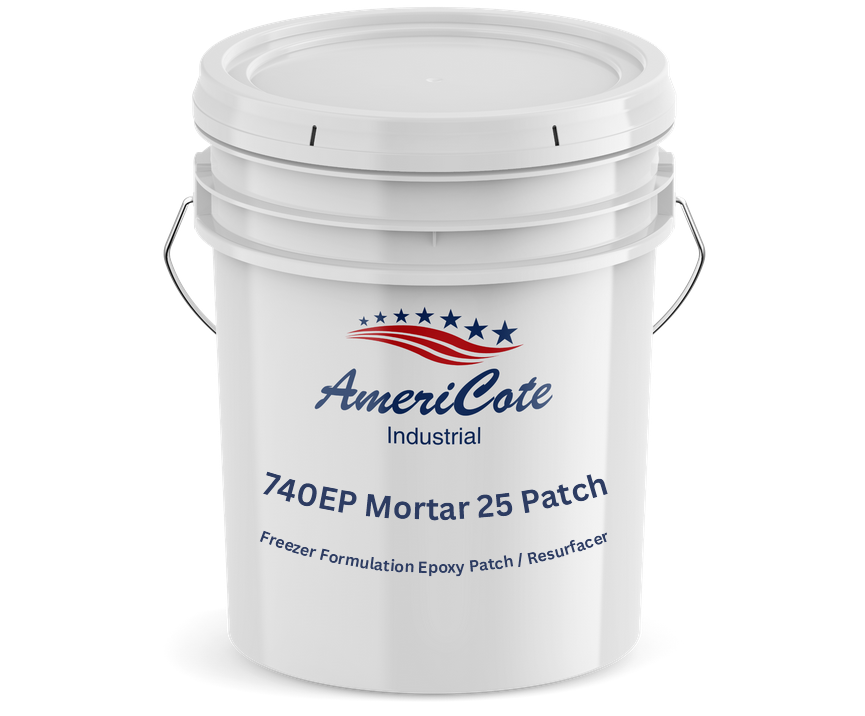
Colors may vary from batch to batch due to variations in the silica filler. Mortar colors are not from our standard color chart. Substrate temperature must be 5°F above dew point. All new concrete must be cured for at least 30 days prior to application. See reverse side for application instructions. Test data based on neat resin.
Physical properties are typical values and not specifications.
See last page for limitations of our liability and warranty. This product has a short pot life, mix only an among of material that can be used in the prescribed pot life period. When temperatures are low, extended time may be required for the material to cure before allowing industrial traffic.
Product Storage:
Surface Preparation:
Product Mixing:
Priming:
Product Application:
Apply the material with a hand trowel or other suitable application equipment. Do not over-trowel the material as this may cause isolated blisters to form. Direct air currrents across or above the mortar during the curing process may result in isolated blisters. Maintain temperatures within the recommended ranges during the application and curing process.
Recoat or Topcoating:
Cleanup:
Floor Cleaning:
Restrictions:
Technical Specifications
Solids By Weight: | 100% |
Volatile Organic Content: | Zero pounds per gallon |
Colors Available: | Light grey, red, dark grey, and natural |
Recommended Thickness: | 1/8” to ¼” |
Coverage Per Unit: | 20.58 sq. ft. @ ¼” and 41.17 sq. ft. @ 1/8” |
Packaging: | ¼ unit .11 cu ft. (approx.) 1/8 unit .43 cu ft. (approx.) *UNIT = 6.25# part A, 37 ounces by weight for part B, 50# aggregate. (Bulks are not available because of the short pot life, all weights are approximate.) |
Mix Ratio: | *UNIT = .67-.68 gallons part A to .25 gallons part B plus 50# aggregate. (weight and volumes approximate) |
Shelf Life: | 2 years in unopened containers |
Abrasion Resistance: | Excellent |
Viscosity: | Part A= 250-320 cps, Part B= 2,500-3,500 cps |
Dot Classifications: |
Part A&C “not regulated” Part B “CORROSIVE LIQUID N.O.S., 8, UN1760, PGIII” |
Flexural Strength: |
10,350 psi @ ASTM D790 |
Compressive Strength: |
7,560 psi @ ASTM D695 |
Tensile Strength: |
6,030 psi @ ASTM D638 |
Ultimate Elongation: |
7.30% |
Impact Resistance: |
Excellent |
Heat Deflection Temp: |
113 Degrees F @ ASTM D648 |
Weathering: |
Good (chalks) |
Cure Schedule:
Pot Life – .45 cu ft. mix | 10 – 15 Minutes |
Recoat or Topcoat | 3 – 4 Hours |
Light Foot Traffic | 6 – 8 Hours |
Full Cure – Heavy Traffic | 2 – 7 Hours |
*Foot Traffic Serviceable | 24 Hours @ 30F |
Application Temperature:
30-80°F
Chemical Resistance:
Xylene | 8 Hour Term – Splash Spill |
1,1,1 Trichloroethylene | 8 Hour Term – Splash Spill |
MEK | Not Recommended |
Methanol | Not Recommended |
Ethyl Alcohol | 8 Hour Term – Splash Spill |
Skydrol | 2 Hour Term – Splash Spill |
10% Sodium Hydroxide | 72 Hour Immersion |
50% Sodium Hydroxide | 8 Hour Term – Splash Spill |
10% Sulfuric Acid | 8 Hour Term – Splash Spill |
70% Sulfuric Acid | Not Recommended |
10% HC1 (aq) | 8 Hour Term – Splash Spill |
5% Acetic Acid | 2 Hour Term – Splash Spill |